
(A human hair is 100 microns in diameter!) Today’s fuel systems require filtration capable of removing particles in the sub-four micron range. We’re not talking about boulder-sized particles. All fuel filters remove some abrasive particles, but many competitive filters are simply not effective at capturing and retaining the particles that are most damaging to fuel system components.

As injector pressures increase, maximum injector life is accomplished by limiting the size and number of particles that get through the fuel filter. How do increased injection pressures ultimately affect you and your equipment from a filtration perspective? Tier 4 fuel systems are highly sensitive to contamination and, as such, require superior filtration. Ten years ago injection pressures were in the sub-10,000 PSI range, today they are exceeding 30,000 PSI. The most prominent design trend is a steady increase in maximum injection pressure in newer diesel engines. When you talk to end users about their filter choices, it’s not uncommon to hear "I’ve used Brand X filters for years and never had any issues." This is not surprising and, in fact, fuel systems in older equipment were more tolerant of contamination.īut as demands for lower emissions, improved performance and reduced fuel consumption have intensified, fuel injection system designs have changed. This level of filtration is equally important in today’s Tier IV engines because more advanced engines demand cleaner systems. The diesel fuel pump utilizes a Cat filter, testament to the quality of filtration found in all Cat filters.
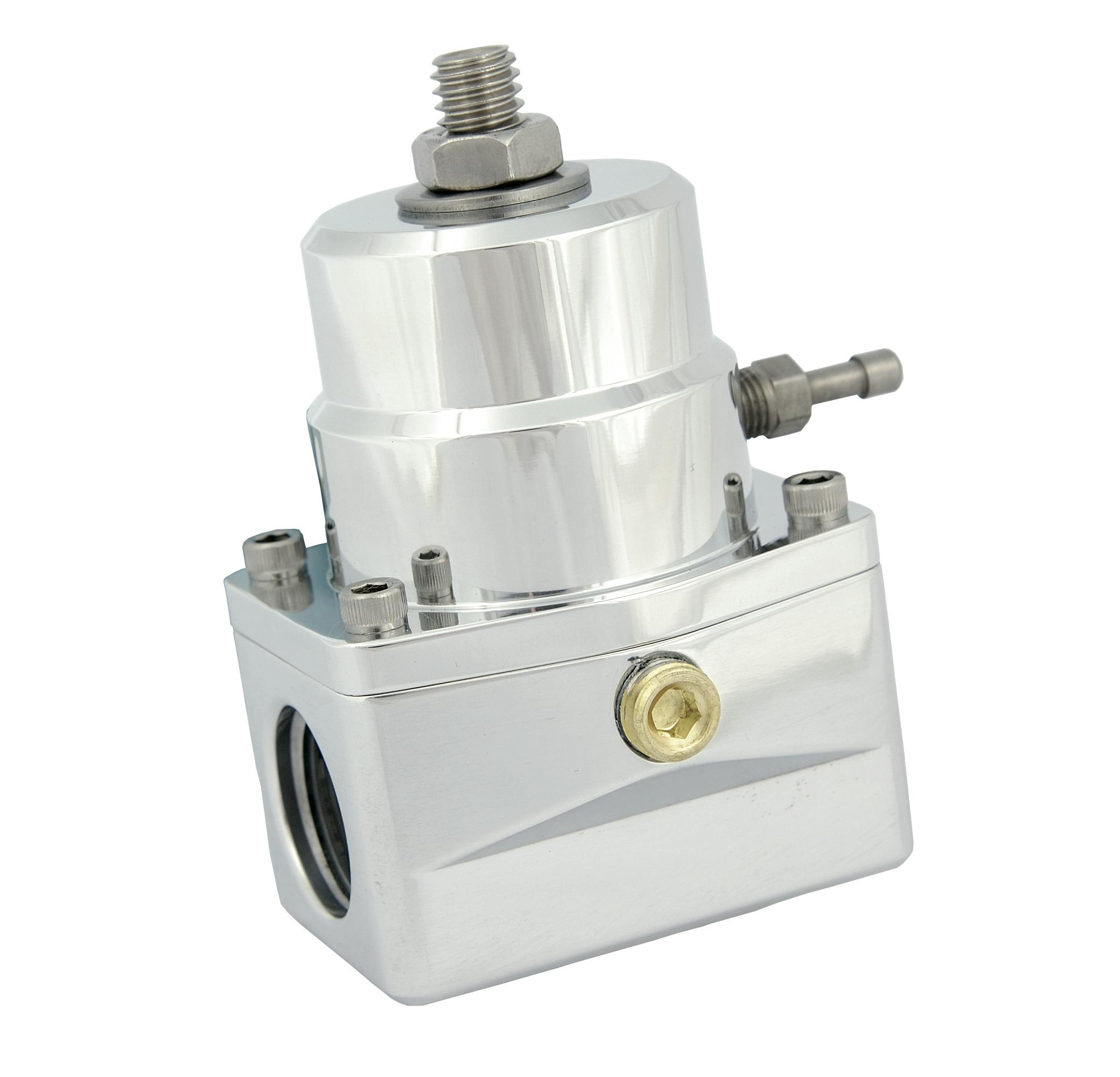
The company was a runner up for Best New Engineered Product at the recent Specialty Equipment Manufacturers Association (SEMA) show in Las Vegas. Aeromotive is the world’s leading manufacturer of high-performance fuel pumps.
